Vibration Testing
Vibration testing in the oil and gas industry involves subjecting equipment, structures, and components to controlled vibrations to simulate real-world operating conditions. This type of testing is crucial for assessing the structural integrity, reliability, and performance of various elements within the oil and gas infrastructure. Vibration tests help identify potential issues related to fatigue, resonance, and dynamic response, ensuring that equipment can withstand the harsh conditions inherent in oil and gas exploration, production, and transportation.
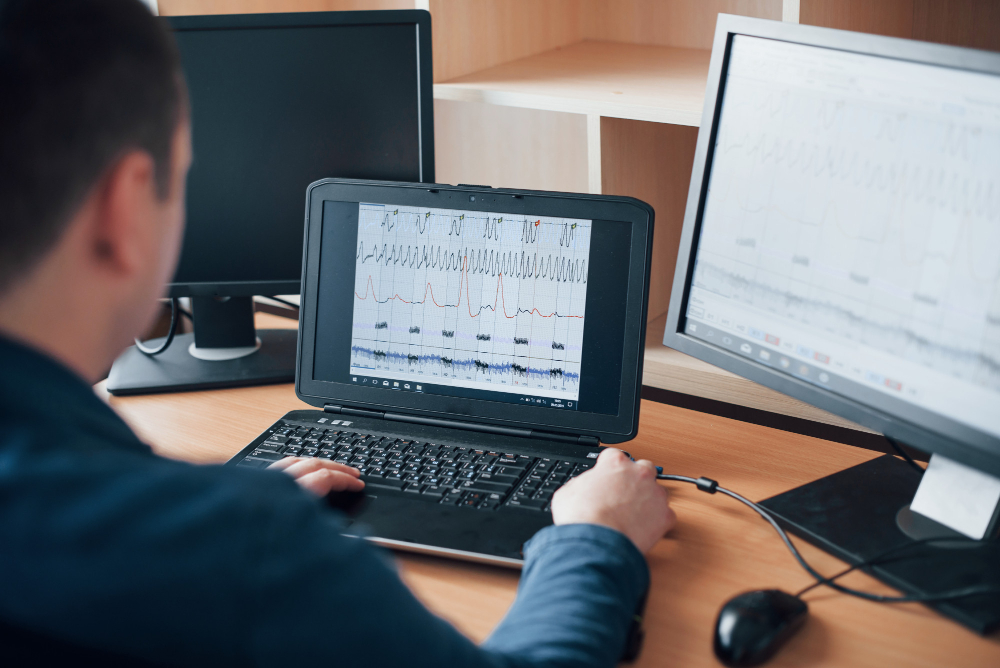
Benefits
Vibration tests are instrumental in evaluating the structural integrity of components and equipment used in the oil and gas industry. This includes pipelines, offshore platforms, drilling equipment, and other critical infrastructure.
The dynamic nature of oil and gas operations, including machinery vibrations and fluid flow, can lead to fatigue failure over time. Vibration tests simulate these dynamic conditions, allowing for fatigue analysis to identify potential weaknesses and prevent premature failures.
Vibration testing helps verify the performance of components under realistic operational conditions. This is particularly important for critical systems such as valves, pumps, and compressors to ensure they can function reliably in the presence of vibrations.
Resonance occurs when a structure or component vibrates at its natural frequency, leading to increased stress and potential failure. Vibration tests help identify resonance points, allowing engineers to design and modify structures to avoid these potentially damaging conditions.
By subjecting equipment to controlled vibrations, engineers can identify and address potential issues before they become critical. This proactive approach to reliability improvement helps prevent unexpected equipment failures and downtime.
Oil and gas equipment must adhere to industry standards and regulations. Vibration testing ensures that equipment meets these standards, demonstrating compliance with safety and performance requirements.
Oil and gas operations involve various environmental conditions, including vibrations from machinery, seismic events, and transportation. Vibration testing allows for the simulation of these field conditions, providing a more accurate assessment of equipment performance.
Assessing the impact of vibrations on equipment contributes to overall safety in oil and gas operations. By identifying potential vulnerabilities, companies can implement measures to mitigate risks and enhance the safety of workers and assets.
Vibration testing helps in predicting potential failure modes and determining appropriate maintenance schedules. This allows for optimized maintenance planning, reducing the likelihood of unexpected breakdowns and improving overall operational efficiency.
Identifying and addressing structural or performance issues early in the design or operational phase through vibration testing can result in cost savings. It minimizes the need for extensive repairs, replacements, and the associated downtime.